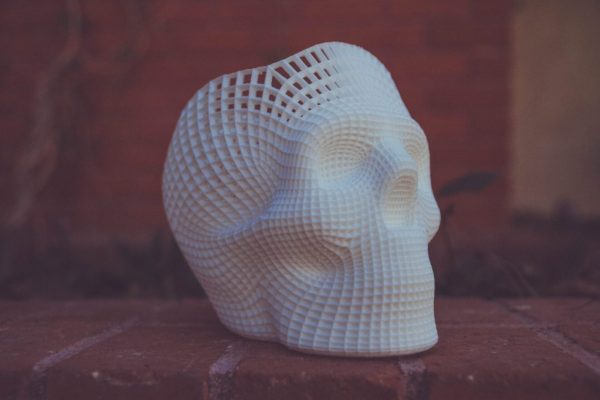
Injection molding is a manufacturing process alongside CNC machining and 3D printing. However, it is costly compared to the other two processes. The highest cost in injection molding technology is the mold cost or the cost of the tools. The time taken to produce the tooling also affects the overall cost. This article describes the tips and factors you need to know when calculating injection molding costs.
How Much Does Injection Molding Cost?
Image source: https://unsplash.com/photos/Epi5exvDtkU
Injection molding is a production technology that injects molten thermoplastic pellets into the molds. The cooled plastic solidifies, and then the mold opens to eject it as a new plastic part. Several factors influence the cost of injection molding. Some factors include the production volume requirements, the product complexity, the material used, and the mold-making process.
Injected material solidifies faster if the mold cools down quickly, allowing you to repeat the production cycle. The cooling process is more critical during large-scale production as it can contribute to low costs. Simple molds that are 3D printed for a small volume production will cost only a few thousand dollars.
Tips for Calculating the Cost of Plastic Injection
Estimating the injection molding costs depend on many variables. Some factors can drive the cost of injection molding up or down. You need to understand the price of injection molding components. The cost of production materials depends on the product design, the material used, and the lot of material filling the mold.
Image source: https://unsplash.com/photos/njf81CyLZEQ
1. Tooling Costs
The tooling costs for injection molding are high and depend on several parameters and design complexities. Factors like living hinges, texture, and inserts influence the prices. They are the highest expense for injection molding manufacturing. The easiest way to control the tooling costs is to order as many parts as you need, which helps each part cost less to make.
The main cost in injection molding is purchasing the mold. Usually, the casts are fashioned using a CNC machining process that comprises aluminum and steel. However, 3D printers and EDM machining processes are also used.
2. Cost of Raw Materials
Materials costs are comparatively small compared to other costs associated with injection molding. The material cost takes about 15% of the mold price. This is because the pellets for injection molding are purchased in bulk.
Several types of plastics are used for the molding process. The cost of these materials varies depending on the specific type of user chooses. Some common plastics are used for injection molding depending on the conditions. Experiment with You can experiment with different materials in the interactive quotes before you start the injection molding process,
Most plastics overlap in strength and functionality, but some are inherently easier to mold, which drives the costs down. The plastic injection molds cost $100 for a 3D-printed low-volume injection mold.
Image source: https://unsplash.com/photos/pQzBUItgf7g
3. Cost of Plastic Injection Molding
Injection molds are available in various sizes, which influences the price. Always consider the part extent, such as how big the party is and whether it will fit comfortably in the mold. Sometimes over-molding can cost you more upfront, but you will have your money later.
Include the part’s size and the location of the facility manufacturing the parts in the hourly cost for machine usage and labor. This means the injection molding costs will be higher if the part is significant.
4. Manufacturing Cost
The manufacturing cost is often 2-3 times the material cost based on the complexity. More complex parts drive the manufacturing costs high, while simple parts without undercuts or advanced surface finishes and more affordable. Every mold considers the risk costs, usually 10% of the mobile price. You also have to consider the package and transport fee.
Image source: https://unsplash.com/photos/bEQRawp1qtY
How to Reduce Injection Molding Costs
You can determine the cost of a mold by the complexity and the time to produce it. The best way to reduce injection molding costs is by adhering to design-for-manufacturing principles. Apply the following design guidelines to reduce the part cost of producing the mold.
Start by evaluating the CAD model’s feasibility before undertaking an injection molding project. Remove potential bottlenecks like undercuts, steep angles, and other complex geometries. The undercard features are complicate and may prevent part rejection.
Second, evaluate the model’s design to eliminate any unnecessary features. This can help reduce mold size and the material used to develop the model. Apply a cockpit approach that simplifies a mold’s design of side B. This approach involves sinking the wall cavities into the mold base to reduce the need to mold steep draft angles while improving the surface finish.
Lastly, use self-mating parts to reduce the need to create multiple molds when one universal mold can achieve similar results.
You can find online injection molding cost estimators or quotes from several injection molding service providers and use them as a benchmark to estimate the cost of injection molding parts. Most of the injection molding cost estimate is to help in the calculation process and have enough experience in the area. They can provide a molding cost comparison table that serves a similar purpose. The injection molding service providers use conversion tables to give customers a rough estimate of the process.
Bottom Line
Injection molding is a manufacturing process only for mass production due to its high tooling costs. There are several factors to consider when evaluating the cost of injection molding is a combination of several factors. You can adjust to lower the injection molding cost if you start with the right formula to calculate the cost per part. This article provides tips on calculating injection molding costs. For instance, use 3D-printed injection molds with benchtops and industrial machines to produce hundreds of functional prototypes.